Packaging Equipment Service: Maintain Your Devices Running Efficiently
Packaging Equipment Service: Maintain Your Devices Running Efficiently
Blog Article
Comprehensive Packaging Equipment Solution to Make Sure Top Performance
In the realm of product packaging operations, the value of detailed equipment solution can not be overstated. By welcoming a proactive maintenance approach, organizations can minimize the risks connected with unanticipated equipment failures.
Significance of Normal Maintenance
Routine upkeep of product packaging equipment is important for ensuring ideal efficiency and longevity. Such maintenance techniques not only extend the life expectancy of the equipment yet also improve functional efficiency. By consistently examining and servicing equipment, businesses can recognize potential problems prior to they rise right into expensive malfunctions, therefore decreasing downtime.
One of the primary advantages of routine maintenance is improved item high quality. Devices that is properly maintained operates even more accurately, ensuring constant product packaging honesty and reducing the risk of flaws. This is particularly essential in sectors where packaging conformity is crucial, such as food and drugs.

Secret Components of Solution
Efficient packaging equipment solution includes several key parts that are necessary for preserving peak operational efficiency - packaging equipment service. Firstly, routine evaluations are essential. These assessments identify damage, making sure that potential concerns are resolved before they rise into costly failures
One more essential element is calibration. Properly calibrated tools assurances accuracy in product packaging processes, which straight impacts item quality and conformity with industry requirements. Additionally, prompt substitute of worn components is crucial; utilizing OEM (Original Equipment Producer) components aids maintain devices stability and lengthens its life-span.
Training workers is just as important. Well-trained drivers are more adept at determining abnormalities and implementing standard procedure, which improves total effectiveness. Additionally, documents of solution documents supplies a historic summary of upkeep activities, facilitating much better decision-making for future solution requirements.
Last but not least, reliable communication with company cultivates a joint method to equipment management, permitting tailored services based upon functional demands. By incorporating these crucial elements, services can make sure that their product packaging devices stays trustworthy, reliable, and qualified of meeting production needs, ultimately contributing to an extra efficient production atmosphere.
Proactive vs. Reactive Strategies
Preserving packaging devices can be come close to with two distinctive methods: proactive and responsive. A positive approach stresses routine upkeep and methodical inspections designed to determine potential problems prior to they escalate. This approach involves organizing routine checks, changing worn-out elements, and implementing upgrades based upon manufacturer referrals. By focusing on avoidance, companies can boost the longevity and integrity of their equipment, lessening the risk of unforeseen break downs that can interfere with procedures.
Conversely, a responsive strategy is characterized by why not check here reacting to problems just after they arise. This method commonly includes attending to tools failures, which can result in considerable downtime and expensive fixings. While some organizations may select this strategy due to perceived price savings, it commonly leads to a cycle of recurring problems and inadequacies. Furthermore, relying entirely on responsive upkeep can impede a business's capability to maximize production routines and satisfy client needs immediately.
Inevitably, the option between aggressive and responsive maintenance methods can dramatically influence the effectiveness of product packaging procedures, affecting both operational performance and general profitability. Taking on a positive state of mind not only safeguards devices efficiency however also cultivates a culture of continual enhancement within the organization.
Advantages of Timely Upgrades
Implementing prompt upgrades to packaging tools can considerably boost operational performance and product quality. Routinely upgrading machinery makes certain that organizations utilize the most recent technical advancements, which can simplify operations and minimize downtime. More recent tools usually features enhanced automation and accuracy, resulting in much faster production rates and decreasing waste.
Furthermore, prompt upgrades can boost conformity with industry requirements and laws - packaging equipment service. As packaging demands advance, outdated devices might not satisfy brand-new safety or environmental standards, risking costly charges and harming a company's track record. Updating equipment not only reduces these dangers however additionally settings firms as sector leaders committed to quality and sustainability
Furthermore, contemporary devices commonly includes advanced tracking systems that supply real-time information. This information can be invaluable for making informed decisions about upkeep, manufacturing scheduling, and inventory management, ultimately driving profitability.
Finally, prompt upgrades can enhance worker satisfaction. Devices that runs efficiently and dependably lowers irritation for workers, promoting a more efficient job setting. To conclude, focusing on routine upgrades to product packaging equipment is important for keeping an affordable edge and making certain lasting success in the marketplace.
Picking the Right Service copyright
Selecting the appropriate company for product packaging tools upkeep and upgrades is essential for making the most of the benefits of prompt enhancements. wikipedia reference An appropriate companion not just makes sure that your machinery runs successfully yet likewise prolongs its lifespan, inevitably adding to your organization's lower line.
When choosing a provider, consider their industry experience and know-how. Search for companies with a tested performance history in servicing the details sorts of tools you use, as knowledge with your innovation can bring about much more reliable services. In addition, evaluate their feedback time and accessibility; a company that supplies timely assistance can reduce downtime and maintain your operations running efficiently.
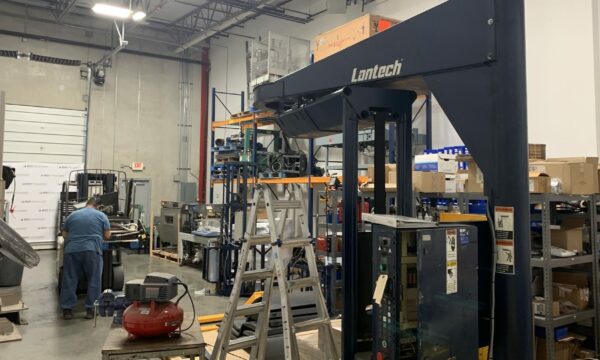
Finally, collect feedback from other customers to determine complete satisfaction degrees and the provider's credibility. By completely vetting potential service partners, you can make sure that you are making an educated description choice that straightens with your operational goals.
Conclusion
Finally, thorough product packaging equipment service plays a crucial duty in keeping machinery performance and longevity. By emphasizing routine upkeep, aggressive strategies, and prompt upgrades, businesses can minimize the risk of unexpected breakdowns while enhancing operational effectiveness. In addition, picking a competent provider ensures that equipment is serviced with OEM components, causing improved product top quality and staff member complete satisfaction. Ultimately, a commitment to extensive servicing fosters a culture of continuous improvement and cost savings within organizations.
Report this page